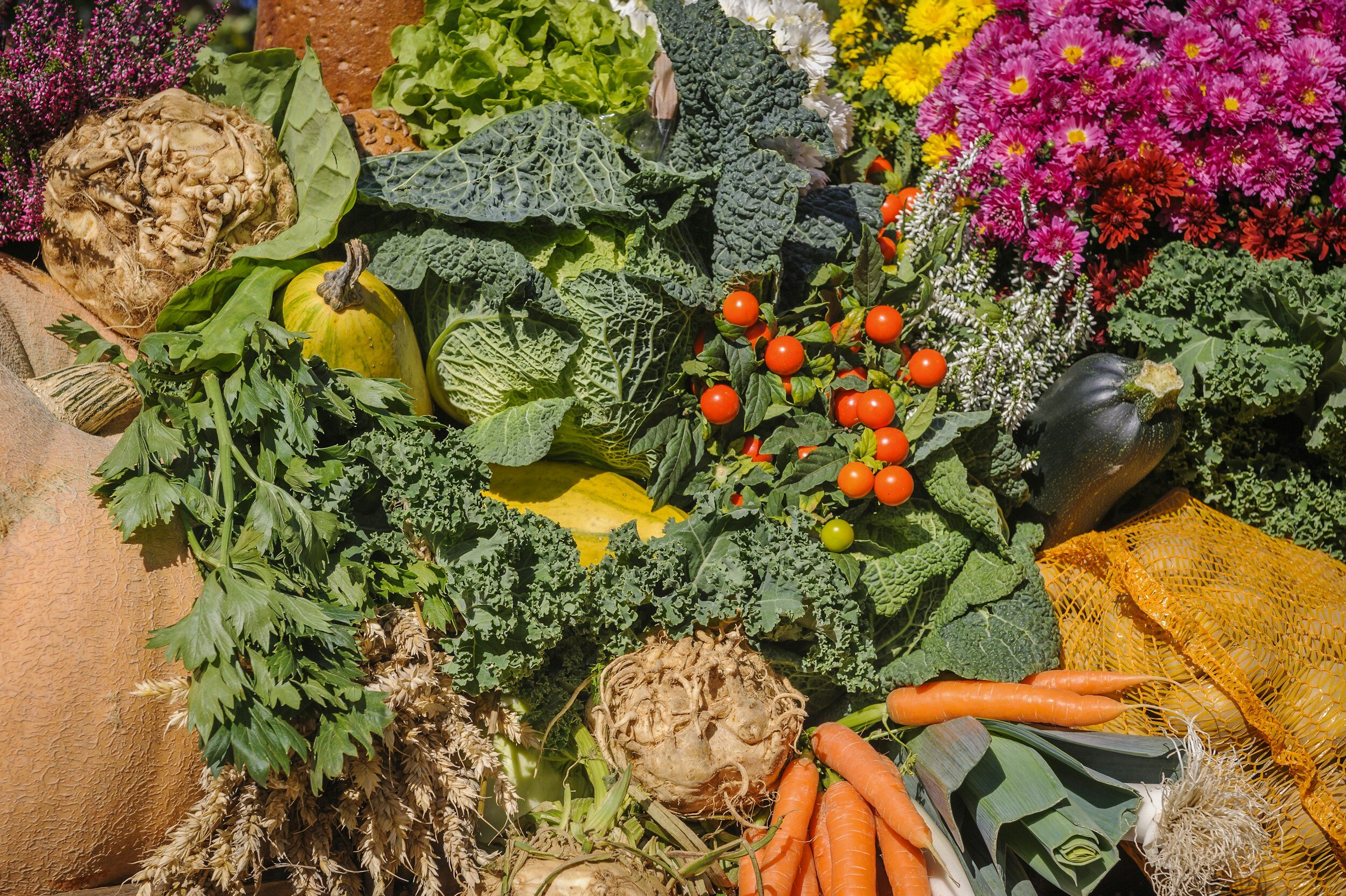
Case Study
Produce & Reduce Program
Reducing Waste in Agriculture by Cultivating a Culture of Sustainability
Background
In 2020, the California Workforce Development Board, through its High Road Training Partnership initiative, offered funding to organizations that could help tackle climate change, improve job quality and promote equity for disadvantaged populations.
Recognized as leaders in workforce development and sustainability in the fresh produce industry, Measure to Improve (MTI) and Equitable Food Initiative (EFI) partnered for the first time on a pilot program at three California agricultural facilities, bringing an innovative approach to building organizational capacity, improving waste management practices and reducing greenhouse gas emissions.
Program Goals
Provide fresh produce companies and employees with the knowledge and skills necessary to develop waste reduction programs and a culture of sustainability.
Reduce the emission of greenhouse gases that contribute to climate change by keeping waste materials out of the landfill.
Pilot Participants
Andrew & Williamson Fresh Produce / GoodFarms Buenaventura Ranch, an open field strawberry farm, Santa Maria, California
Misionero leafy greens packing and processing facility, Gonzales, California
Windset Farms® tomatoes and cucumbers greenhouse operation, Santa Maria, California
Establishing Green Teams
MTI and EFI have experience addressing organization-level challenges in the fresh produce industry by using diverse teams.
Following an approach that brought strengths from the MTI model of developing a Green Team of representatives from multiple departments and the EFI model of creating worker-management collaborative teams, each pilot site established a Green Team with diverse membership customized to meet its organization’s internal needs.
Teams included 12 to 20 members from upper-level management, accounting and data analysis, human resources and training, operations management, field/plant supervision, facilities maintenance and frontline planters, pruners, harvesters and janitors.
90% of the green team members represented categories of staff, managers and admin
10% represented upper-level management
Process
Training & Implementation
MTI and EFI led the Green Team members at each pilot site through training sessions and hands-on activities to build their capacity to develop and implement a waste reduction plan. Teams were encouraged to identify waste-related problems or opportunities and design solutions to fit their organizations as they progressed through the training and activities.
Green Teams conducted their own physical waste audits, sorting and weighing the contents of an entire landfill container. Based on this data, teams then determined which materials could be reduced, reused, recycled, composted or otherwise diverted from the landfill, and they prioritized actions in their waste reduction plan.
Pilot Program Training Topics
General background on sustainability, climate change, greenhouse gas emissions and waste reduction
Waste audits to assess material streams and opportunities for waste reduction
Waste reduction plan development and implementation
Data collection and analysis of the volume and cost of waste streams over time
Communication of the goals and actions of the waste reduction plan to the workforce
Use of data and problem solving for continuous improvement
Results
The Produce & Reduce pilot program approach was developed around the idea that the success of an organization wide waste reduction program would depend on the engagement of the entire workforce to effectively implement changes.
The three waste reduction plans developed through this program reflected the diversity of challenges and perspectives unique to each organization; however, all plans shared the need for employee engagement at all levels of the workforce.
Program participants agree that the Green Team model provided the organizational structure and communication systems needed to support a shift toward a culture of sustainability, where employees are empowered to think critically about waste reduction and understand their role in maintaining a system that leads to less waste, reduced costs and lower greenhouse gas emissions.
The three pilot participants continue to track and improve their materials use programs and plan to conduct annual waste audits to gauge progress and identify new opportunities.
By The Numbers
50 Number of people trained directly by MTI and EFI
2,557 Estimated number of indirect trainees
144+ new tons Total volume of materials kept out of landfill
435+ MTCO2e Total reduction in greenhouse gas emissions (equivalent to 1,080,454+ miles driven by an average gasoline powered passenger vehicle)
Testimonials
“Implementing Produce & Reduce has helped us increase efficiency and generate long-term business value by fostering a culture of sustainability and responsible resource management. By investing in our workforce through such training programs, we are creating a lasting positive impact on the bottom line and the environment.”
Johnny Arriaga, Senior Plant Operations Manager, Misionero
“This project was a natural fit for GoodFarms. Investing in sustainability is a core value for the company because it simultaneously improves the quality of our products and the quality of lives by protecting our ecosystem and preserving natural resources for future generations.”
Amalia Zimmerman-Lommel, Director of Social Responsibility, GoodFarms
We have saved money and generated funds through increased recycling and waste reduction programs. Every single company should get started, because there are financial savings along with positive environmental impacts.”
Jeff Madu, Vice President of Sales, Windset Farms
It was rewarding to see how far-reaching this program was. Members from the participating organizations prided themselves on sharing and educating their neighbors, families, and friends on placing materials in the proper containers. Everyone was doing their part to reduce the negative impacts food loss and waste has on the environment. This waste reduction program was a perfect example of incorporating all three pillars of sustainability – people, planet, and profitability – and how to approach sustainability initiatives moving forward. It starts with assembling a Green Team, data collection, and goal setting, then follows the training and internal and external communications.”
Nikki Cossio, CEO & Founder, Measure to Improve
About Measure to Improve
Founded in 2014, Measure to Improve’s mission is to help produce companies measure, improve, and credibly promote their sustainability efforts. Our clients include produce growers, packers, shippers, and industry associations across the United States. Our staff has a proven track record of helping companies identify and implement strategies to increase efficiency. By supporting clients in setting ambitious, but attainable, sustainability goals, MTI encourages progress that can be validated and marketed. MTI’s projects address a variety of sustainability challenges, including water, energy, greenhouse gas emissions, waste, and social accountability.
Special Thanks
Support from the California Workforce Development Board allowed Measure to Improve (MTI) and Equitable Food Initiative (EFI) to join forces with forward-thinking companies that were willing to invest significant time and resources to strengthen their waste reduction programs. Through this pilot, the companies discovered passionate sustainability champions within their workforce who can be developed as leaders.